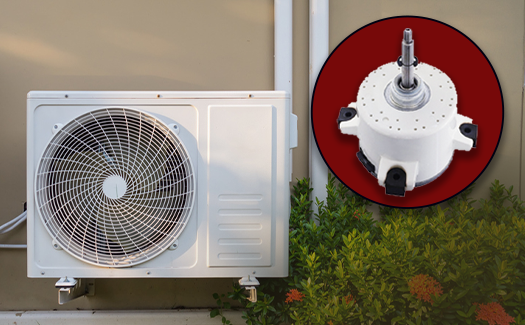
Case Study: Development of a Compact Motor for Ergonomic Strengthening of Side-Discharge HVAC Outdoor Units
- HVAC/R & Appliance Devices
The objective is to reduce the number of motors used in the outdoor unit.
To develop a motor with 20% more output than a conventional motor of the same size.
Typically, these small side-discharge-type outdoor units for commercial air conditioners are manually transported from the point of delivery to the installation site. Since the conventional units are large and heavy, the ergonomic stress of manual transportation can be laborious and exhausting.
The electric fan motors installed in the outdoor unit directly affect the system's total weight and the job's demand. Our development of a new motor with higher output allows a real decrease in the number of motors in one system, directly contributing to a significant workload reduction.
Objective
To reduce the total weight by using fewer motors in an outdoor system while maintaining performance and a low profile.
Typical applications of outdoor units are installations in well-ventilated locations that are not exposed to rain or direct sunlight. Those locations are often too small to use a cart for easy transportation and, as a result, are sometimes carried manually to the installation site. An outdoor unit is typically 1.5 m (4.9 feet) in height. This size can hinder the vision of laborers carrying the unit. In addition, the typical weight of the system is approximately 100 kg (220 lbs) and imposes a large, strenuous load on the workers who are required to transport it. By developing a fan motor with increased performance at a similar size, the Outdoor system can now consolidate from the conventional 2-motor installation to only a single fan motor. As a result, the HVAC is reduced in both size and weight.
Solution
A complete redesign of the motor core magnetic structure.
In concept, consolidating to only one fan motor in the outdoor HVAC system would require a larger motor and fan to keep the same air volume output. However, using a larger motor would conflict with the new design concept by increasing the weight of the outdoor unit. A deeper look and approach to the motor design were necessary to solve this problem. The design solution came with intuitive changes to the magnetic core of the motor. One improvement example was an increase in the number of poles in the magnetic circuit. Magnetic flux was also improved by revamping the core shape. A final improvement consisted of a redesign of the magnets which resulted in increased output of the motor performance without any increase in the size of the motor’s outside diameter. One potential issue of the new motor design, having increased power at the same size, was the increased risk of the rotor magnets cracking due to vibration. The adoption of anti-vibration material in the new rotor structure also resolved this.
Improved magnetic flux, achieved by increasing the number of poles and redesigning the core and magnet shape.
Vibration-absorbing material, low-vibration structure.
Increased Output
The increased number of stator poles and optimized core shape delivered greater torque. Furthermore, the magnet shape was revamped for the improvement of magnetic flux.
Vibration Suppression
Using vibration-absorbing material and employing a low-vibration structure successfully achieved advanced results of vibration suppression.
Magnet Cracking Prevention
The magnet shape was changed to better align the outer rotor wall, which also increased torque and reduced vibration.
Newly Developed Product
Features of the AR-9H Motor
- Rated output: 70 to 180 W
- The number of poles increased to 10 to achieve high efficiency and low vibration
- Equipped with the vibration-resistant rotor (measured against torsional resonance)
- Application: Multi-split air conditioning systems
Feedback
Comments from the motor development Engineer
To eliminate the total quantity of motors used and realize an increase in the output of a single motor, we brainstormed and critiqued the conventional design meticulously. In our achievements, we increased the number of poles in the magnetic circuit and tweaked the core's shape and changes in the rotor magnets. Increasing the motor output without any increase in size resulted in new issues, such as vibration and the risk of the magnets cracking. We achieved the target performance output without increasing the motor's outside diameter. Risks of vibration and cracking of the magnets were resolved by adding vibration-absorbing material and employing a low-vibration structure of the rotor core. Our new motor helps reduce the outdoor unit's size and weight, thus decreasing the ergonomic workload on laborers. We hold a great sense of fulfillment from knowing that our new motor is a product that contributes to society. Our business principle is that we continue developing motors that deliver such benefits to our customers.