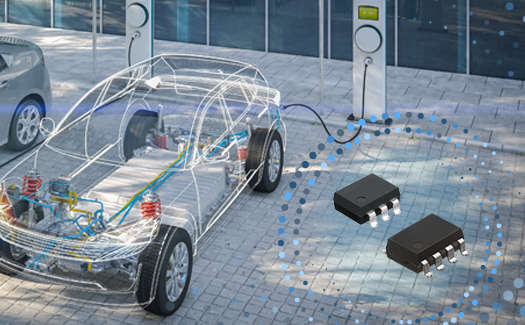
Driving Innovation: How Panasonic is Revolutionizing the Automotive Industry with PhotoMOS® Technology
Published on- Relays & Contactors
The article discusses the use of PhotoMOS® in various automotive applications, including Battery Disconnect Units and Inverters, highlighting its space-saving design, high voltage support, and ability to prevent contact welding. It also emphasizes the importance of derated voltage for ensuring reliability in automotive designs. PhotoMOS offers fast, quiet, and bounce-free switching, with almost unlimited switching life and extreme reliability in harsh conditions. Panasonic provides specialized automotive-grade PhotoMOS with double molding insulation for durability.
Panasonic's PhotoMOS® Technology: Revolutionizing the Automotive Industry
The global automotive industry is an essential part of the global economy, playing a vital role in the development of roads, fuel stations, and transportation systems. This has created a need for innovative new technology, leading Panasonic to develop highly reliable and long-lasting devices for a variety of applications within the automotive market. One of these devices is our PhotoMOS®, which enables fast, quiet, and bounce-free switching in miniature sizes. These devices have an almost unlimited switching life and offer extreme reliability in cases of shock and vibration. The benefits of this technology have positioned Panasonic as a top provider of PhotoMOS® solutions in the automotive market.
Panasonic offers two types of control relays: mechanical relays and semiconductor relays. Mechanical relays use movable contacts, whereas semiconductor relays, also known as PhotoMOS®, use an LED input coupled with MOSFETs as the switching elements. Within the PhotoMOS® product line-up, Panasonic offers a specialized type specifically designed for automotive usage. The internal construction of an automotive-grade PhotoMOS® features double molding insulation, which allows for more durability in harsh environments.
Applications: Leak Detection
There are several applications in which PhotoMOS® are used, including Battery Monitoring Systems, Inverters, Battery Disconnect Units, and EV charging. In Battery Monitoring Systems, PhotoMOS® can be used for both Battery monitoring and leakage detection. Leakage detection is crucial in monitoring the battery’s health to ensure long life and maximum performance over time. In the event of leakage when the PhotoMOS® is on, the current sensor detects a high voltage ground-fault current signaling an alarm output.

Measure leak detection using PhotoMOS® in a Battery Monitoring System.
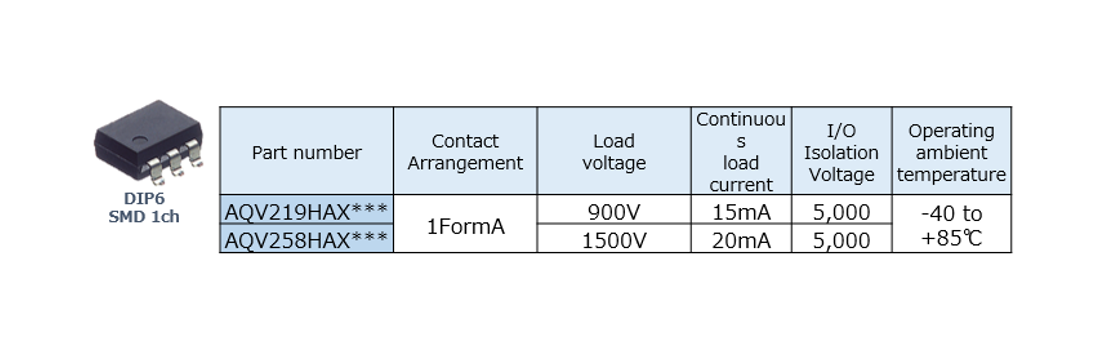
Recommended PhotMOS® part numbers for Leak Detection and Battery Disconnect applications.
Applications: Battery Monitoring
In battery monitoring, the high input/output isolation voltage capability of PhotoMOS® can be used in a circuit to measure the charging voltages of a battery cell. This is achieved by charging and discharging a capacitor load bank. When compared to traditional mechanical relay or discrete solutions, PhotoMOS® offers a longer life, a simplified circuit design, occupies less board space, and has a singular guaranteed specification.
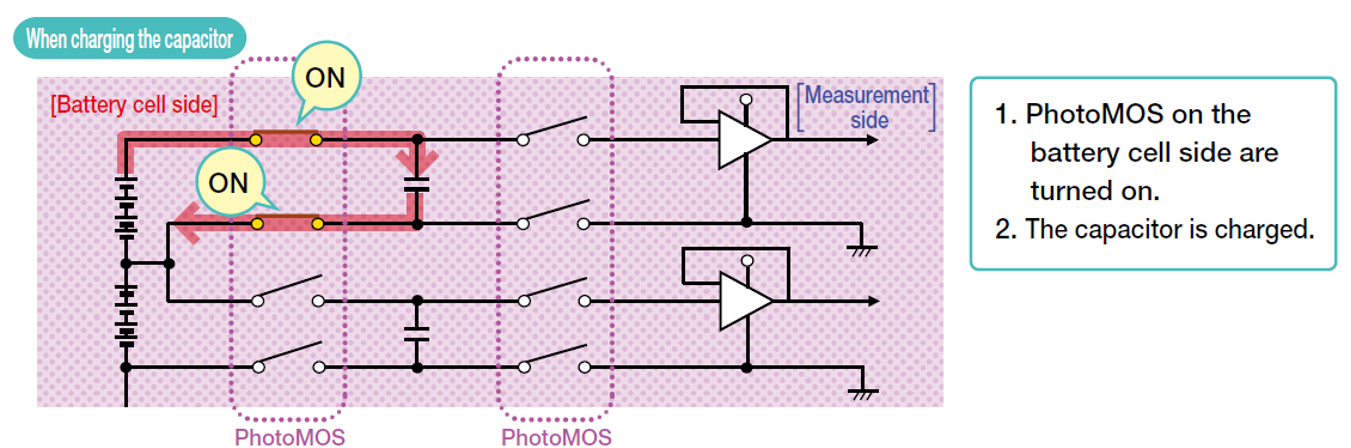
PhotoMOS® for Battery Monitoring: charging the capacitor.
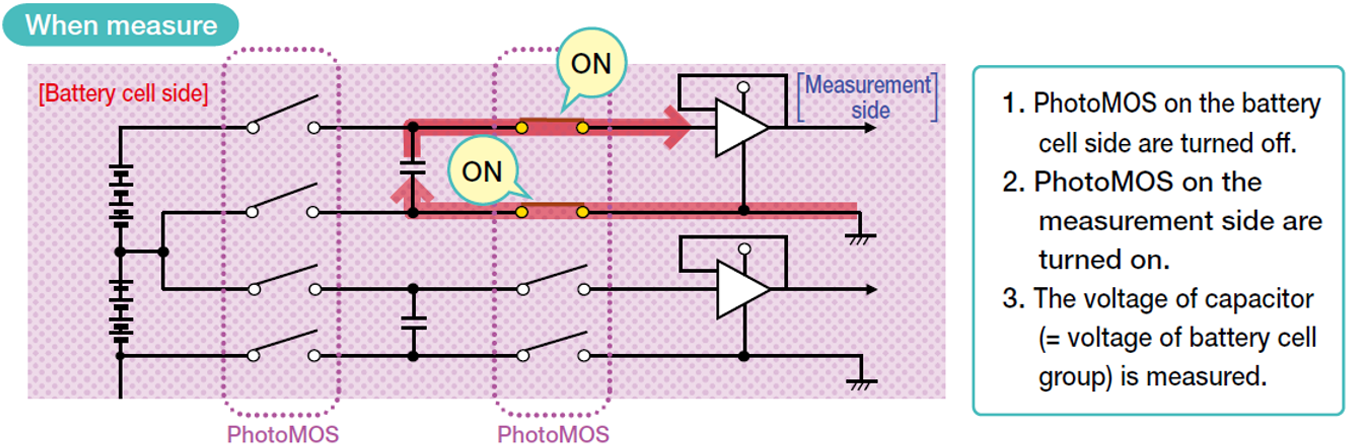
PhotoMOS® for Battery Monitoring: measuring.
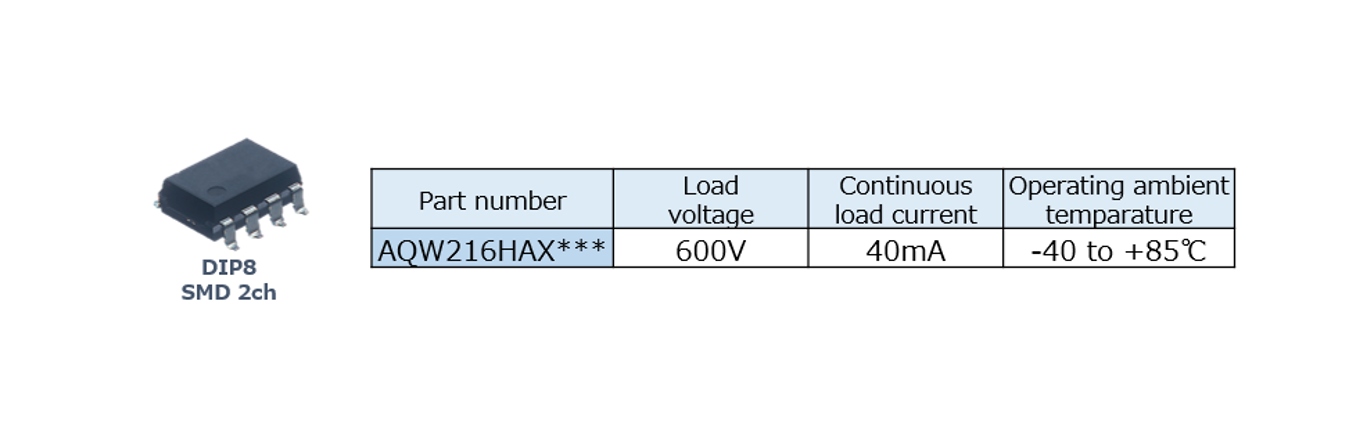
Recommended PhotoMOS® part number for Battery Monitoring applications.
Applications: Battery Disconnect Unit and Inverter
In the Battery Disconnect Unit, PhotoMOS® is utilized for Relay welding detection. In this application, PhotoMOS® provides space savings, supports up to 900V, and prevents contact welding.
In the Inverter, PhotoMOS® is used for switching the DC link discharge. Traditional solutions use Gate Drivers, which typically require larger, complicated circuits. In contrast, PhotoMOS® provides a circuit design with fewer components, eliminating the need for an additional power supply line and using capacitors, resistors, and Zener diodes. Additionally, PhotoMOS® offers space-saving and support up to 900V.
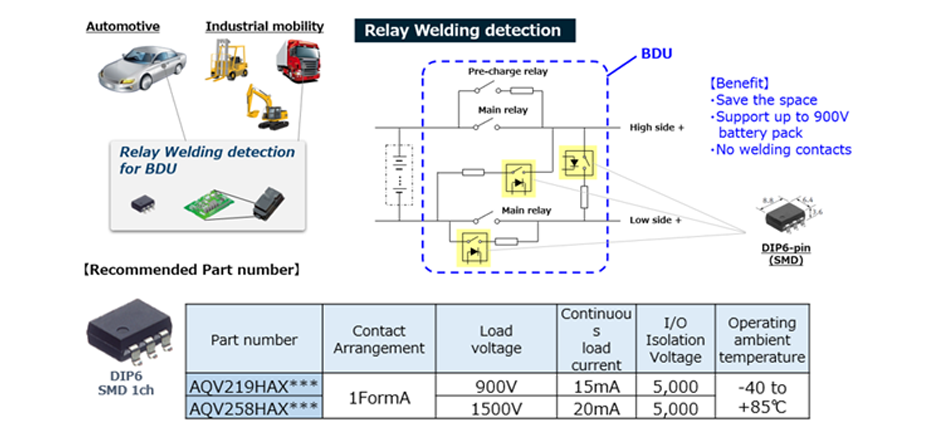
PhotoMOS® for Relay Welding Detection
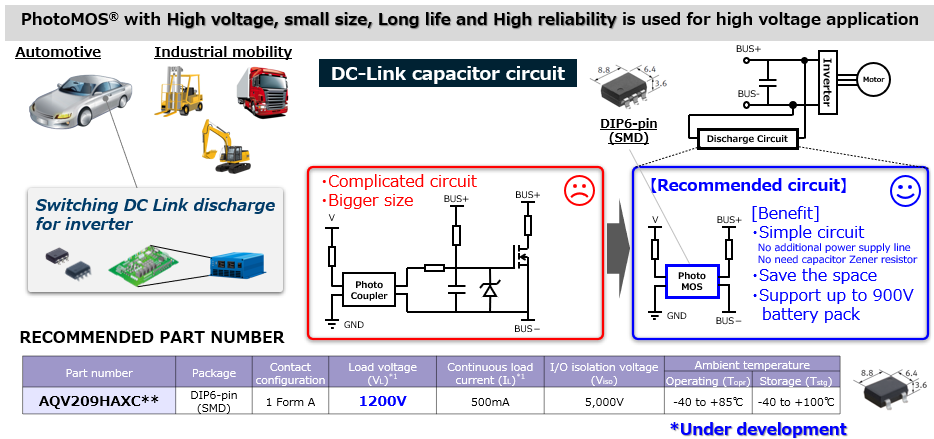
PhotoMOS® for Inverters
Design Consideration
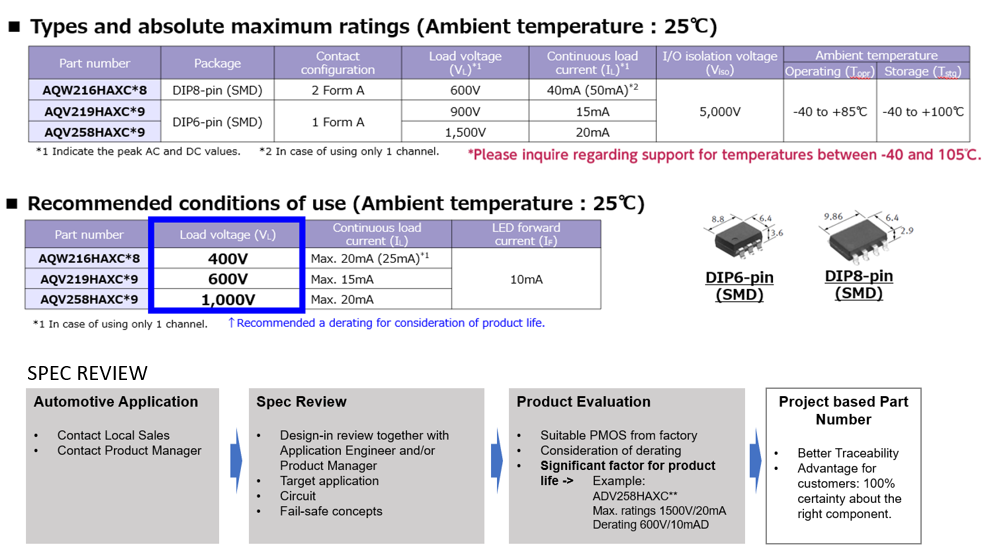
Summary
When choosing devices for automotive use, it is crucial to incorporate an appropriate safety margin during the design phase. One important factor to consider when using PhotoMOS® Semiconductor Relays in automotive applications is the derated voltage. Derating is vital in ensuring the proper function and long life of any reliable automotive design.
To choose the most suitable PhotoMOS®, it is recommended to seek guidance from a Panasonic sales representative and engineer before integrating the products into automotive environments and completing a spec review. This step is necessary to prevent potential performance, quality, and reliability issues in vehicles. Panasonic is dedicated to developing technology that not only offers high performance but also guarantees long-term reliability throughout the product's lifespan.
Contact us about PhotoMOS® today!